Magnetic Coupling
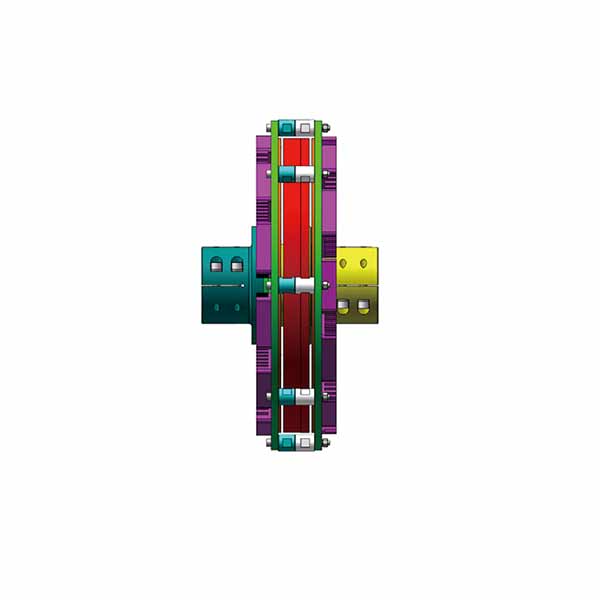
Standard Coupling For Small Power (OS Series)
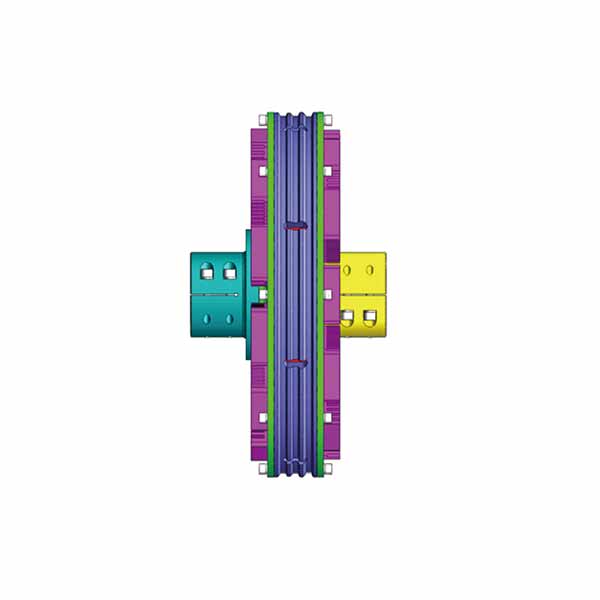
Standard Coupling For Big Power (OFS Series)
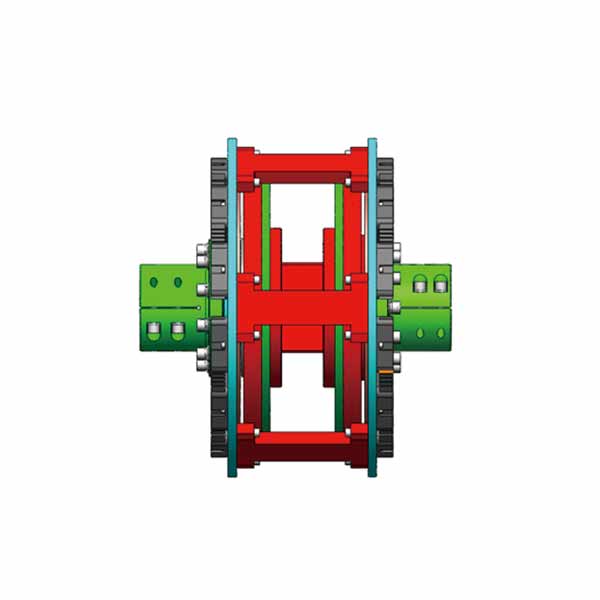
Torque Limited With Small Power (OX Series)
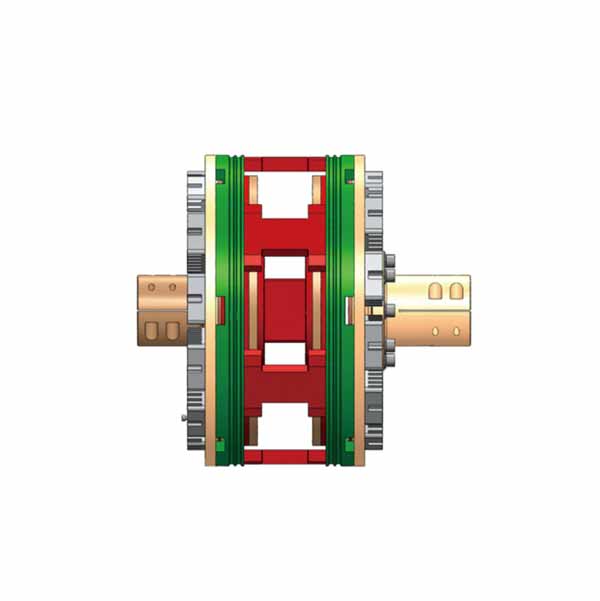
Torque Limited For Big Power (OFX Series)
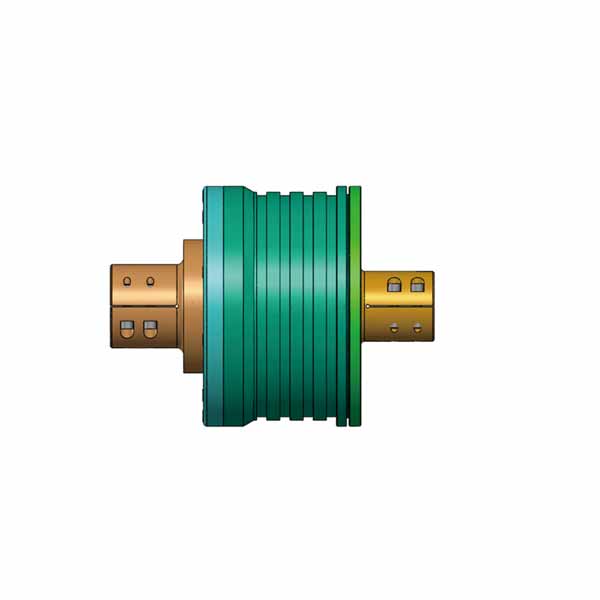
Synchronous Magnetic Coupling (OTB Series)

Mining Magnetic Coupling (BX Series)
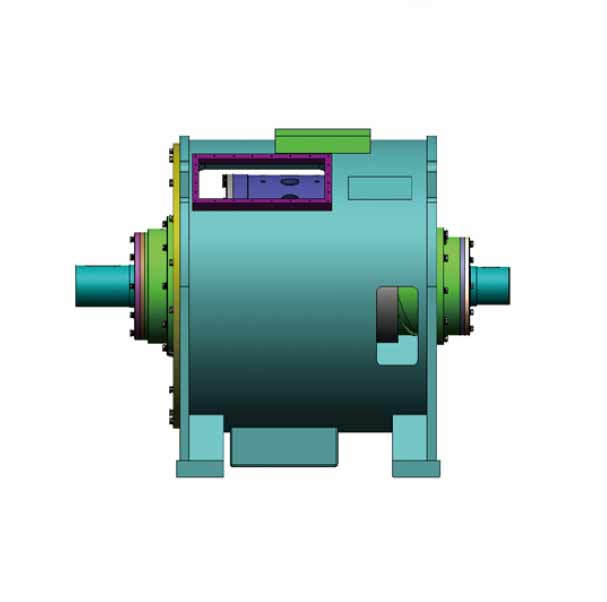
Adjustable Speed Magnetic Coupling
Drum Magnetic Coupling
Magnetic coupling began to become an alternative to liquid couplers. That is very popular these years. People can find these couplings anywhere like mining, cement plants, oil and gas facilities, and coal plants.
What is magnetic coupling?
The coupling on this website is a coupler that can connect a large motor and transfer high torque. The torque can be transferred without touch by using magnetic couplings. The magnetic coupling we are talking about is different from the magnetic drive pump.
How does magnetic coupling work?
By magnetic driving rotor working, torque is transmitted magnetically to another rotor. You can put a few thin wooden plates between the two rotors will not affect the transmission of torque.
Which kind of magnets be used?
Most couplers on the market use NdFeB and SmCo. Because they transfer high torques and are also resistant to high temperatures. Because of the different working principles, some couplers will get hot during operation.
Structure
These powerful couplings have 2 types of structure, disc type, and drum type. Whether it is synchronous or eddy current, there are disc and disc structures.
In conclusion
The magnetic coupling has a wide variety of uses. It is reliable, efficient, and cost-effective. It is an ideal choice for applications such as conveyor belts, crushers, and more. With advances in technology, the magnetic coupling will become more famous and popular. Choose this coupling for your next project for reliable, long-lasting torque transfer.